
A square can have one dimension for an edge and that dimension once changed will be used for all for example for sweep along a path you can make a construction plane that flows along a pathĪnd where the path and cPlane intersect is always the sketch x/y 0 sketch engine uses a solver to adjust sketches like when you add a length dimension and change the value it scales the line.Ī dimension can also be shared. You can draw quickly a square like shape, then add 4" dimensions to the lines and then to horizontal and vertical edges add vertical/horizontal constraintsĪlso the center point of a sketch is for parametric modeling important. In your example with a 4" x 4" square you can draw a line to 4 inches horizontally while using grid snapping So for readability the idea of constraints is pretty amazing - it also replaces functions like rotating something in a sketch. If no constraint is there I would have to measure the angle first. You as a user have to make the call when what tool and function will be best used without blindly following some CAD ideologies.Ĭonstraints in general can also be very helpful when you open a sketch and you see two lines have a 70 degree angle constraint.
AUTODESK GRAPHIC LINE WITH ROUNDED ENDS FREE
This is were traditional parametric sketch modeling ideas collide with free form surfacing workflows and each on thinking they are superior. Sometimes instead of dimensions I just use the lock icon so parts of sketches cannot move. Sketch changes will result to surface changes. It is a pain to adjust a design when having to always adjust dimension values (face palm process) vs push n pull spline fit points to much faster evaluate how On the other side as long as you know what you do not everything has to be also constraint. In Alias Rhino and such where there are constraints and I can move something of a sketch and nothing else will be adjusted or influenced. Think of constraining like stabilizing your sketch so when you edit a value the solver will adjust the sketch you want and not how the solver might think. It is this situation that troubles me at this point in my design to manufacture reason for fully constraining a sketch is simply - unlike cad apps that do not use a solver Fusion uses a solver and thus the sketch is like a house of cards. We want the parts to be exactly like our design, but we need to give the shop some freedom to change it. How does constraining our drawing help us when we transition from our design to the shop who will make the parts for us. As I understand it, selecting a k factor has an influence on things like bend allowance and bend deduction. If " all sketch elements are properly constrained and dimensioned so they cannot freely move", there is still nothing to stop the new sheet metal shop design from having a different k factor and corner relief from my design. So you have two designs then, mine and the sheet metal shop's. This design must match what I created in my design. Then the shop takes my design and creates their own design which they will use to produce the parts. If I did not, then there would be no sheet metal design. As I understand my function as a designer is to assume a value for these and incorporate them in my design. This concerns the k factor as well as things like the corner radius details which are dependent, as we discussed before, on the quality of the tools used by the sheet metal shop.

I see a possible problem here, at least in my case. I often use "Infinity Pool" and there sketch elements turn black. For a single 3D printed object this might not of much importance but when you build a manufacturing machine with hundreds of components, under constrained and not fully dimensioned sketches can lead to very costly disasters, when things don't line up.įusion 360, depending what screen background (Environment) you use choose, colors fully defined (constraind and dimensioned) sketch elements differenty to let the user know that this is fully defined. My earlier comment is related to sketches only.Īs the elemental building blocks, if these are not fully defined, meaning all sketch elements are properly constrained and dimensioned so they cannot freely move, this can easily break a design. Many people unfortunately use the term drawing when referencing a model. This is a technical drawing and in Fusion 360 can be created by making a drawing from a component group (assembly) or a single component.

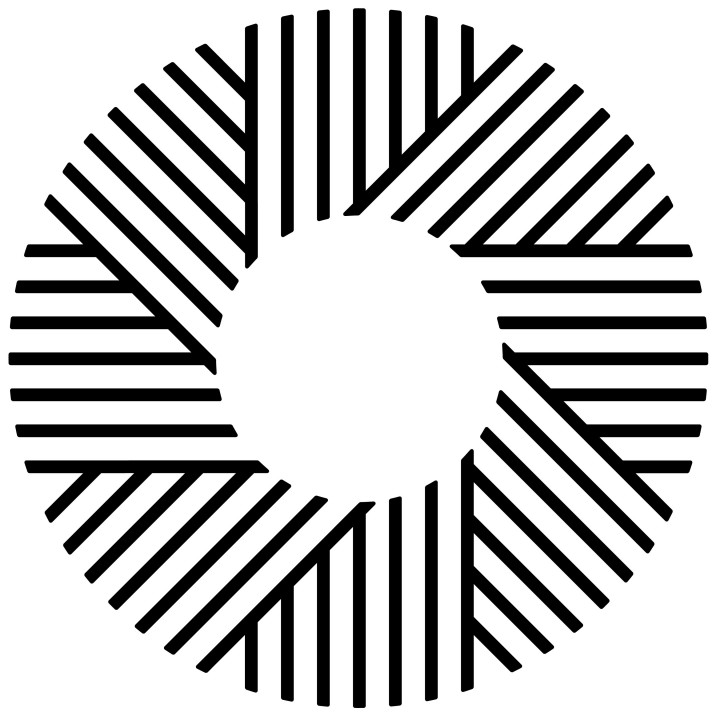
360 also often referred to as the design constitutes 3D geometry. They are mostly created to serve as the basic outline of geometry.Ī model, in Fusion. So let me clarify the usual use of this terminology, which is also reflected in the Fusion 360 user interface:Īside from T-Splines and the primitives in Fusion 360 (Box, Cylinder, etc.) sketches are the only way to create 3D geometry Fusion 360.

Yes, this is likely a terminology issue at least to some degree.
